Fusion5 offers a comprehensive range of solutions, including ERP systems designed to support manufacturers (with features like predictive maintenance and automation), through to planning, data, and analytics solutions and services that enhance planning and forecasting, CRM (customer relationship management) solutions to drive sales and customer relationships, and service improvement and support solutions. Additionally, we offer cloud-based human resource software to ramp up recruitment, training and retention.
Our reliance on local manufacturing and supply chain management depends greatly on which side of the ditch you reside. If a day at the beach involves a pair of thongs and an esky full of your favourite stubbies, then sure, you could be forgiven for thinking it's dead. But if jandals and a chilly bin full of cold ones are more your 'culture', then you may feel a little more confident in a career in the manufacturing industry.
In reality, the two nations are far more aligned than you may think, and the opportunities are equally lucrative for manufacturers who can seize these opportunities in 2025 and beyond.
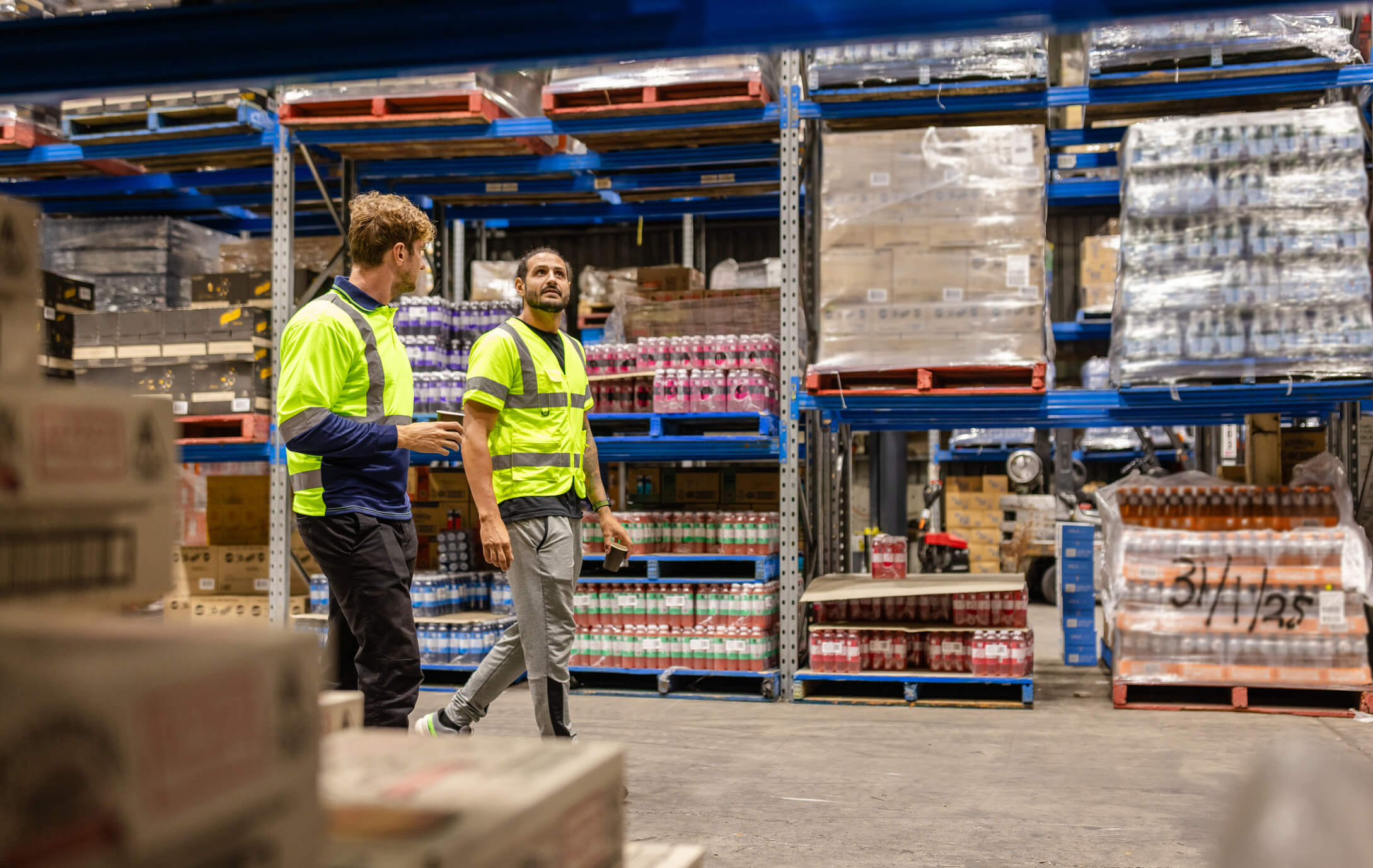
Key takeaways:
- Hopes for supply chain consistency are still on a distant horizon…far, far away.
- Shortages of skilled workers will negatively impact sector growth and ability to compete.
- Rising power costs and uncertain continuity of supply have the potential to impede the sector’s ability to compete.
- It will be business-critical to invest in and leverage new technologies to compete effectively and offset resource issues.
1. The supply chain is far from sorted
While we all acknowledge the havoc that COVID-19 wreaked on our supply chains at the time, we have yet to see the problems dissipate. Around 60% of Australian businesses report that they are still impacted by material delays and are bearing the brunt of disrupted production schedules and increased costs.
So, what’s causing this degree of chaos?
Among other issues, disruptions can be attributed to bottlenecks in global transportation resulting in the delayed delivery of essential components, surging uncertainty and concern caused by geopolitical and global trade frictions, a continuing deluge of natural disasters, rising shipping costs (which impact profit margins) and limited domestic alternatives for specialised components.
Likewise, in their March 2025 planning forecast, BusinessNZ warns New Zealand manufacturers that supply chain issues still loom large, especially given the geopolitical tensions caused by punishing tariffs and wars. They quote the IMF (International Monetary Fund), who said: “An intensification of protectionist policies, for instance in the form of a new wave of tariffs, could exacerbate trade tensions, lower investment, reduce market efficiency, distort trade flows, and again disrupt supply chains.”
In their efforts to overcome the ongoing impact of an inconsistent supply chain, more than half (55%) of Australian manufacturers said they intended to re-shore their operations in Australia by 2023. This move has been supported by the Australian Government through its Modern Manufacturing Strategy. (However, come 2025, we have yet to see any research which confirms or denies the sector’s success in re-shoring.)
It seems the only safe prediction when it comes to supply chain consistency is that it will remain inconsistent. And the manufacturing industry will have to factor in how to manage or live with the consequences.
2. The people problem persists
In the 1960s, approximately 25% of Australia’s working population was employed in the manufacturing industry. Today (2025), Australian manufacturing contributes approximately 6% to the national GDP and employs over 850,000 people (6.1% of the workforce).
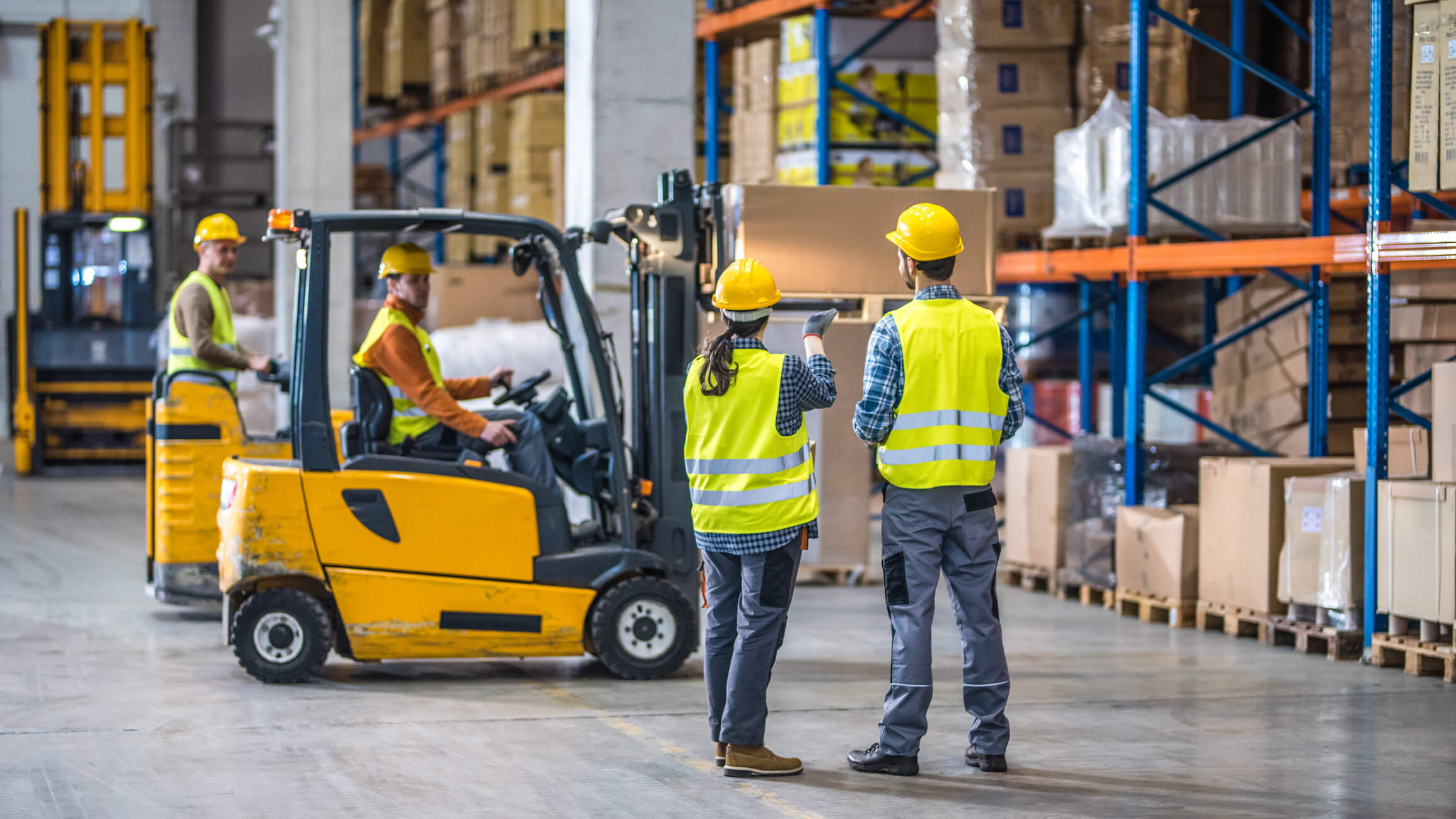
As for 2025 in New Zealand, after nearly two years in decline, the employment drought in the manufacturing sector appears to have broken. According to the latest BNZ – BusinessNZ Performance of Manufacturing Index (PMI), New Zealand’s manufacturing sector displayed expansion for the first time in 23 months and is at the highest rate of growth since September 2022. In 2025, the sector is expected to contribute around 10% to New Zealand’s GDP and employ over 230,000 Kiwis – accounting for 10% of the workforce.
Both countries, however, are faced with manufacturing workforce shortages. Skilled workers are in short supply, especially as the increasingly sophisticated sector has an increased reliance on employees who are au fait with roles that simply didn’t exist a few decades ago. These include digital technology operations and programming, advanced machinery maintenance and repair capabilities, automation supervision, sustainability management, and data analysis and interpretation.
“NZ manufacturing industry screaming out for skilled workers,” according to The Manufacturer’s Network. They go on to comment on the issues caused by an ageing workforce and a lack of talent entering the sector. The urgency of the shortage is such, they add, that there has been a growing search for skilled labour, including talent from overseas, to ensure NZ’s manufacturing industry remains competitive in a global market.
As for Australia, manufacturing is impacted, alongside construction, technology, supply chain, and technical services by (continuing) workforce shortages. According to AI Group, 71% of Australian industry leaders expect to be affected in 2025 and “Industry leaders report shortages across both lower- and higher-skilled roles, which negatively impact productivity, growth and financial performance.”
On the positive side, says Australian Manufacturing, “Initiatives like the National Skills Agreement aim to align training with industry needs, while automation and robotics adoption help bridge the workforce gap.”
In the meantime, these shortages lead to issues such as reduced production capacity, production delays, missed growth opportunities, and competitive disadvantages – both locally and globally.
3. Power costs are a drain on the industry, and sustainability is on the rise
In a sector heavily reliant on an affordable and uninterrupted energy supply, increasing costs continue to damage bottom lines.
With grid infrastructures on both sides of the ditch in need of upgrades, power reliability poses a real risk to production capabilities. And it opens the doors to even more competition from low-cost production countries like China, more technologically advanced European nations, or competitors with advanced automation.
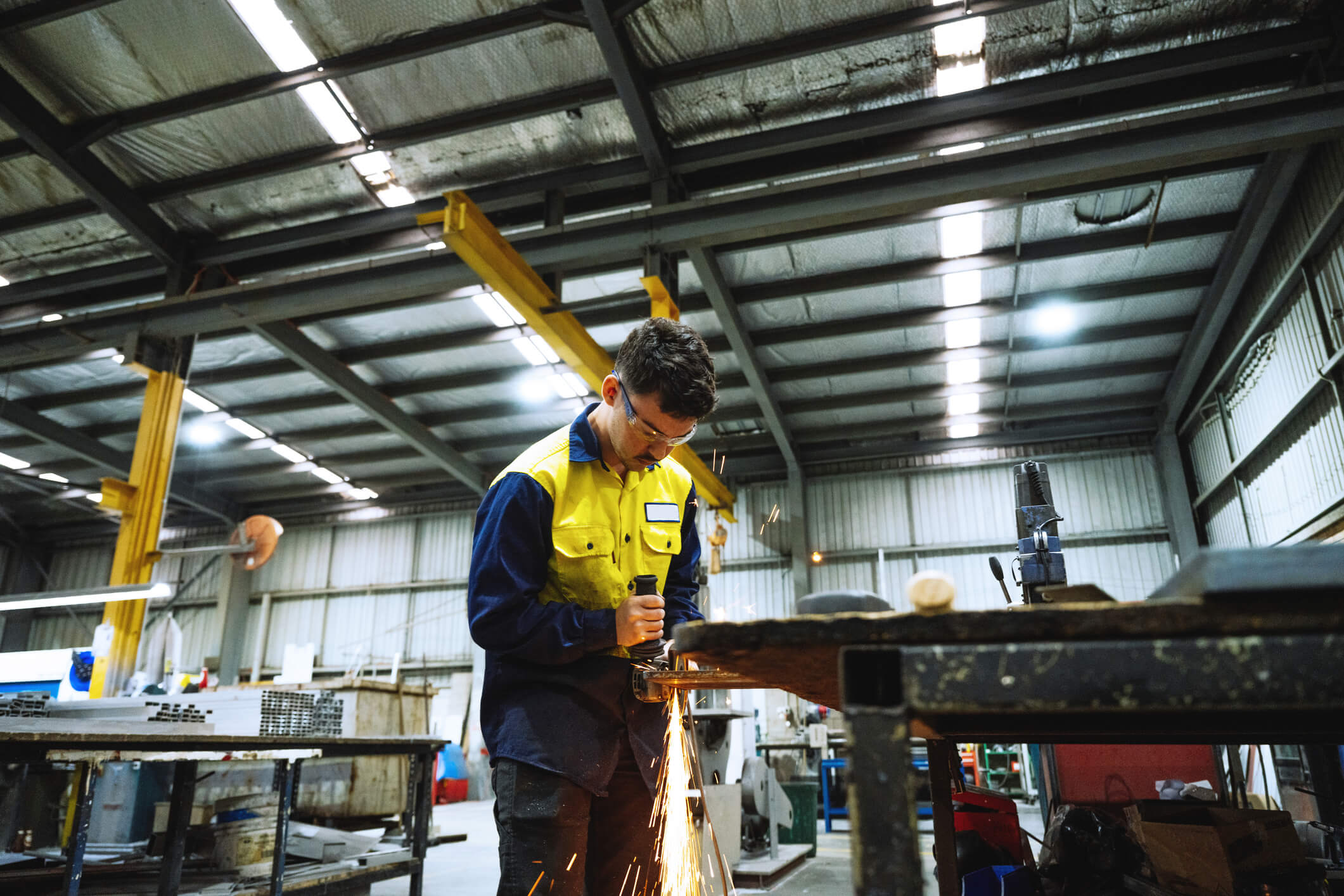
Infometrics reports that in New Zealand, manufacturing activity is the most exposed to higher energy costs – with primary metal and metal product manufacturing first in the firing line, followed by chemical and dairy product manufacturing. Leading Kiwi manufacturers, including Methanex, NZ Aluminium Smelter, and Pan Pac, have been forced to curtail their operations (temporarily and, in some cases, permanently) as a result.
Things are equally tough in Australia. According to MacroBusiness, Australia has no manufacturing future, saying: “The reality is that Australia’s manufacturing sector can only remain competitive with affordable and reliable energy. And Australia has no energy future if gas and electricity prices rise.” They cite closures such as fertiliser manufacturer Incitec Pivot (2022) and Qenos, Australia’s last significant plastics manufacturer (2024). The closure of Qenos made Australia wholly reliant on imported plastics from China. To top it off, in January 2025, Orica, the world’s largest provider of explosives and chemicals for mining and fertilisers for farming, threatened to wind down its operations in Australia and invest in the US instead.
However, there could be a sustainable light at the end of the tunnel with projects led by companies like Fortescue Future Industries showcasing the potential of green hydrogen and other cleaner energy solutions. In March 2025, the Australian Government announced $750M in grants to advance the development of low-emission technologies in metals manufacturing, with a focus on hydrogen-based iron production. Other initiatives include the Hydrogen Headstart program and the Powering the Regions Fund, which aim to stimulate the clean energy sector.
As for New Zealand, the government has tabled a Fast-track Approvals Bill, which lists 22 renewable electricity projects dedicated to increasing New Zealand’s electricity capacity generation by almost 30%.
The only hope is that initiatives like these aren’t too late for an already beleaguered industry sector.
4. Technology holds the key, but who's walking through the door?
The idea behind offshoring some or, in many cases, all our supply chains was to save money on labour.
But throw into the equation Agentic AI, Robotic Process Automation (RPA), Artificial Intelligence (AI), Machine Learning (ML) and Augmented Reality (AR) and the cost efficiencies of offshoring your supply chain are becoming obsolete. Who would have thought the costs of hiring a robot here are near-equal to hiring one overseas?
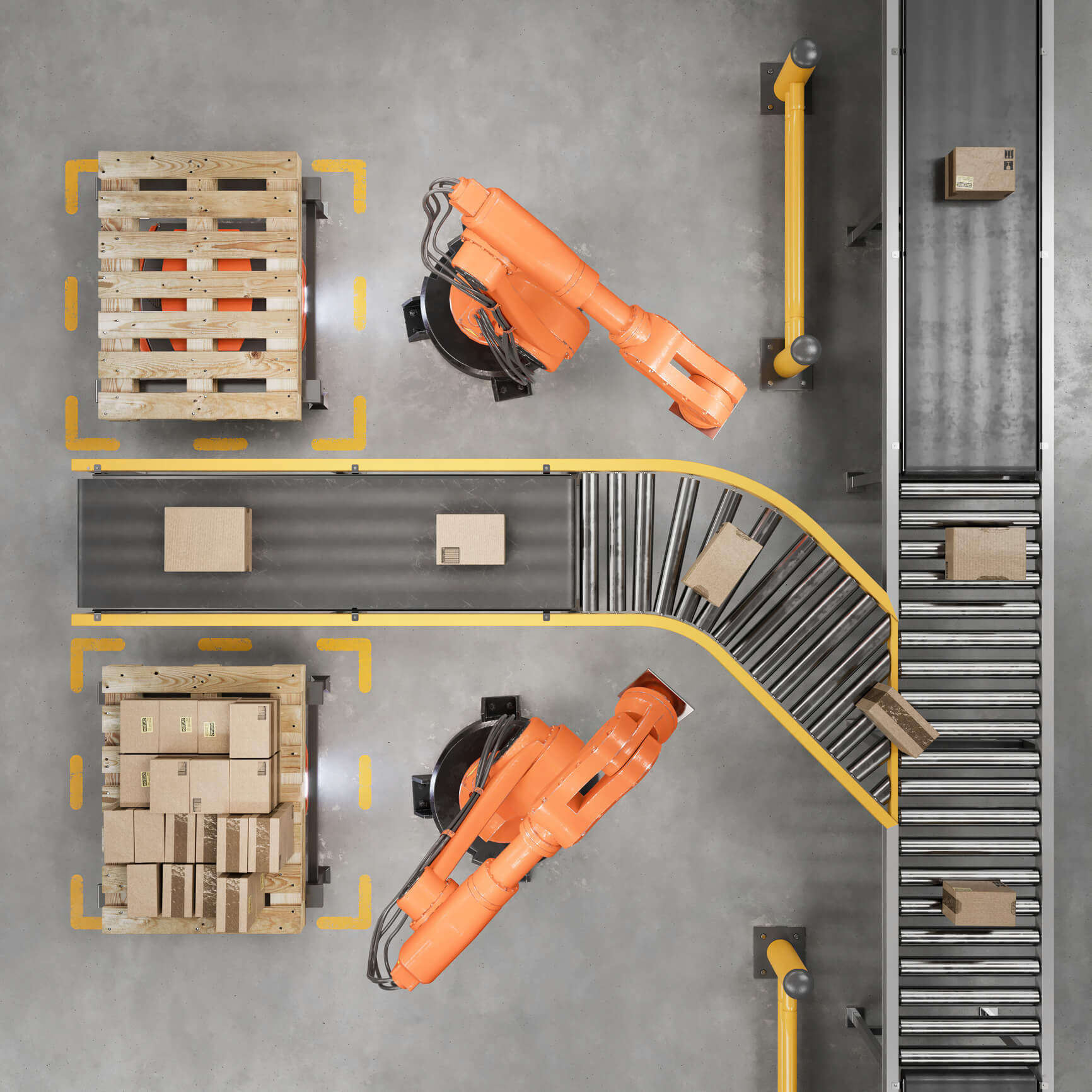
As of last year, over 36% of Australian businesses had already adopted AI or automation technologies – and manufacturing was one of the leading industries to do so. Everything suggests that Kiwi manufacturers are also exploring and adopting new technologies – which is timely. According to NZ Manufacturer, Kiwi manufacturers are at risk of losing ground if they fail to invest in automation and productivity improvements.
While emphasising the need for effective orchestration, ITBrief described Agentic AI in manufacturing as a game-changer for Australia (with the manufacturing and mining industries leading the charge in Agentic Automation adoption). The article says manufacturers will “achieve significant productivity gains and return on investment through agentic automation's ability to monitor and assess vast amounts of streaming data and then decide, plan and execute actions in real time.” And that they will be enabled to “autonomously manage supply chains, inventory levels, equipment maintenance, demand forecasting (including for JIT manufacturing), quality assurance and logistics planning.”
In its 2025 Manufacturing Industry Outlook, Deloitte also recognises the advantages to manufacturers in adopting AI-driven automation, predictive maintenance, and smart manufacturing technologies – and the positive impact these technologies will have on workforce shortages and efficiency.
What are some examples of manufacturers leveraging AI automation?
These manufacturers and distributors are successfully leveraging Microsoft Dynamics 365 to thrive.
A collaboration between Thyssenkrupp and Microsoft has led to the development of the elevator industry’s first real-time, cloud-based predictive maintenance system. The system can accurately predict in real-time when an elevator is going to fail and notify an engineer for repair, meaning far less risk of people being trapped inside and the ability to schedule maintenance resources ahead of time.
Toyota is another example. The business invested in a significant expansion of its local distribution and warehousing. Toyota Australia has built one of the country's most advanced automotive distribution centres, a multi-million-dollar robotic process automation facility in Western Sydney, housing more than 100,000 automotive parts for both local and export markets. Meanwhile, Toyota New Zealand's expansion warehouse has increased from 24,000m² to 35,000m², allowing them to supply their network of dealers with more than 95% of daily orders directly from the shelf for overnight shipping.
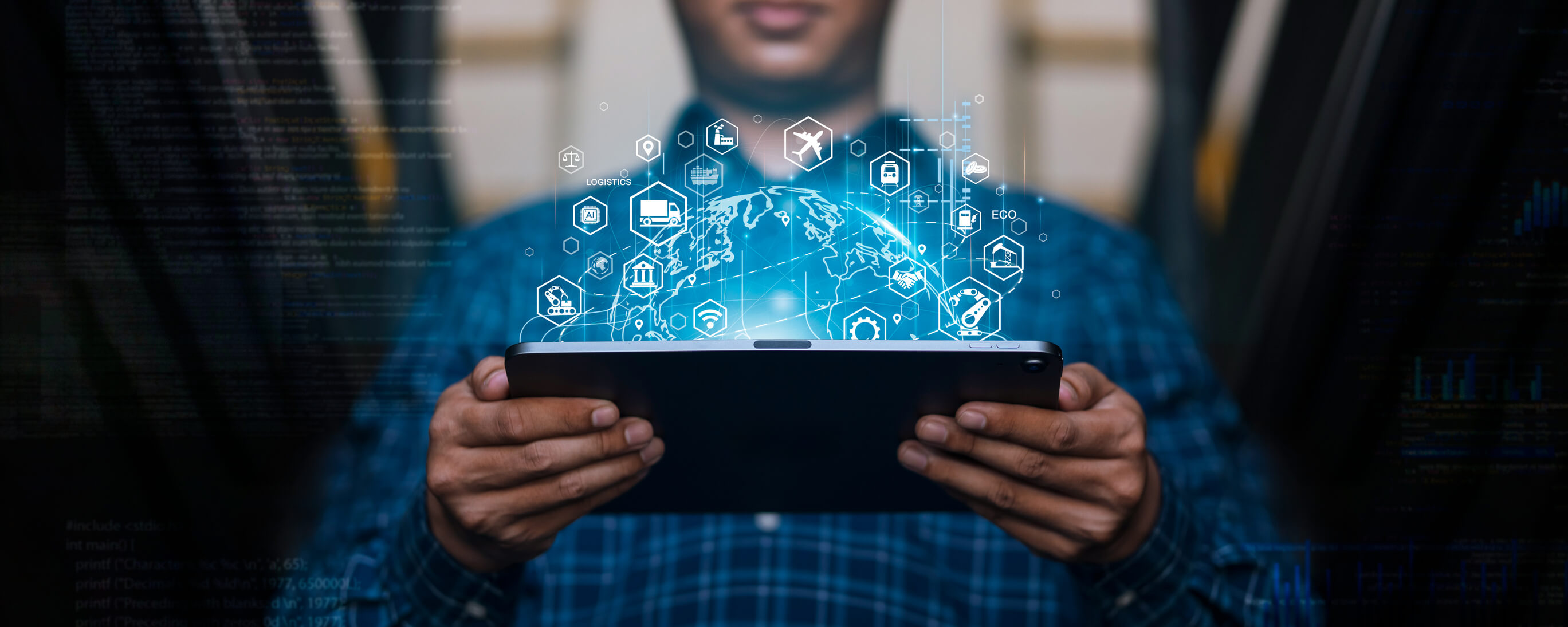
Lastly, Jabil, a manufacturing solutions company, has leveraged Microsoft Azure's Machine Learning technology for its 'Factory of the Future' initiative, which adopts cross-functional workstreams and automation across the entire facility. The primary goal of the initiative was to create a system that can automatically identify and correct faults in the manufacturing process as they arise.
The results? First and foremost, humans have been removed from the mundane and repetitive nature of controlling quality as they tirelessly scan through image after image of the same parts. Instead, their robots now eliminate 72% of pass-through components without manual intervention and capture 92.18% of true defects.
As standard now, businesses are benefiting from a unified view of stock, warehouse, manufacturing, service, and logistics with Dynamics 365 Supply Chain Management. But with a greater reliance on advanced technology comes a greater demand for the skills required in maintaining that technology in order to stay competitive. And here, we circle back to the shortage of skilled resources, as discussed in point 2.
While robots are not replacing humans, they are freeing them up to do human-specific (and less mundane) jobs. In many ways, automation isn’t a threat to human jobs but a lifeline – offering employees the opportunity to learn and upskill in a digital world.
Summary
While manufacturing in Australia and New Zealand is far from its deathbed, it is certainly under significant pressure. While the price of power is largely beyond the control of most businesses, our respective governments have introduced significant initiatives and are committed to assisting.
But as for skilled resource shortages and supply chain issues – you’re on your own.
However, by investing in the right technologies – from a comprehensive ERP to Agentic AI – you can address these challenges or at least mitigate their impact and sharpen your competitive edge while others struggle to keep pace.
FAQs
What manufacturing solutions does Fusion5 offer?
How does Fusion5 help manufacturers overcome supply chain challenges?
The leading ERP systems we offer enhance supply chain management by integrating processes across departments, providing real-time data access, and improving inventory management. This improves supplier relationships and demand forecasting, leading to optimised planning and scheduling. Fusion5 also helps customers bridge supply chain challenges with existing solutions through highly effective, robust system integration.
How does Fusion5 support AI and automation adoption in manufacturing?
We help manufacturing customers transform their businesses by adopting new ERPs with AI and automation capabilities, enabling a 'smart enough' approach to digital modernisation. Automation can streamline production planning, inventory management, supply chain operations, and more. We leverage AI and machine learning functions to help automate tasks, predict issues, and optimise processes.
What success stories or case studies showcase Fusion5's impact on manufacturers?
From replacing ageing, disparate on-premises technologies to helping drive stronger customer relationships, Fusion5 has helped our manufacturing customers generate some stellar results, including a 30% growth without increasing headcount for Natural Pet Food Group. We transformed stocktaking accuracy and real-time visibility with Advanced Warehousing and mobile scanning for Metroglass, improved Steel & Tube’s ability to follow up and convert customer quotes, as well as removing the risk and complexity of running legacy systems for Snell Packaging.
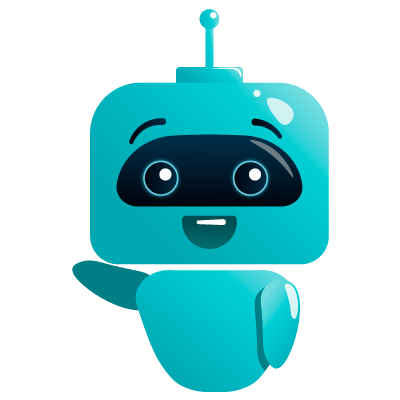